Boost Workplace Safety: Your Guide To Electrical Test And Tag
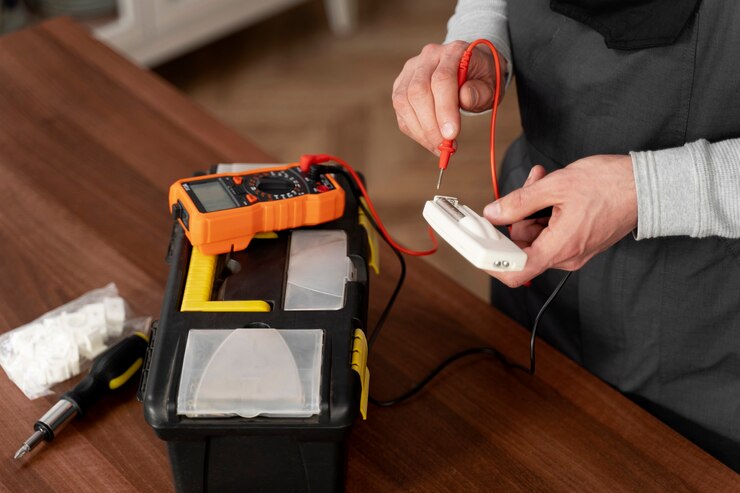
Have you ever entered a workplace and felt a little uneasy about the tangled mess of wires and the age of certain appliances? You’re not the only one. Workplace electrical accidents, though too often downplayed, are a severe issue. A wonky toaster, an electric extension lead all frayed around the ends – these seemingly minor problems can cause serious injury, fires, and deaths. And that’s where electrical test and tag and electrical safety inspections Melbourne businesses rely on can be helpful. A health check for your electric equipment, so to speak.
A complete visual inspection and electrical testing of all your portable plants are needed to ensure they are safe to use and that your people and your company are safeguarded from harm. This handbook includes everything you want to know about electrical tests and tags, from procedure and regulation to best practice, all within the new AS/NZS 3760:2022 standards.
What is an electrical test and tag?
Electrical test and tag is a two-part process that helps ensure the safety of portable electrical equipment. It’s similar to taking the car into the garage for a service, but rather than getting the oil and tyres serviced, we get it serviced for electrical faults.
- Visual Inspection: This is the first and often most faults are found. An experienced technician will visually check the appliance carefully for any outward damage, such as frayed cables, cracked cases, loose cables, etc.
- PAT Testing: If the eyesight test passes, the appliance is tested electrically using a Portable Appliance Tester (PAT). This helpful tool tests earth continuity, insulation resistance, and leakage current—all the electrical doohickeys and bits and bobs that can cause problems if they’re not of the highest quality.
After a tested appliance is labelled, it’s not a pleasant sticker; it’s a record. It states who tested it, when it was, and when it’s due for its next test. Record-keeping isn’t only good for compliance but also suitable for substantiating your commitment to workplace safety.
Why are electrical test and tag important?
Electrical testing and tag are good things to do; they are the law. An employer is responsible for ensuring the workplace is safe, and part of that is ensuring that electrical equipment is secure.
- Legal compliance: Legal tests and tags aren’t always a strict piece of legislation to adhere to (more information below), but it’s better to be safe than sorry and prove yourself to comply with your duty of care. Non-compliance can result in massive fines and potentially even prosecution if anything goes wrong.
- Safety first: The primary reason for testing and tagging on a priority basis is safety. Faulty electrical equipment can cause electrical shocks, burns, and fires. Regular testing and tagging minimise these risks, protecting your employees and business.
- Peace of mind: When you know your electrical equipment is safe, you are at peace. You can operate your business without fear of electrical hazards.
Who needs an electrical test and tag?
Though other companies have strict legal requirements regarding test and tag, the rule applies to every workplace.
- High-risk workplace: Construction, demolition, and mining operate in extreme conditions. Their electrical tools are susceptible to damage. These industries usually operate with frequent testing schedules, typically as often as three months.
- All workplaces: Even if you are not working in a dangerous enterprise, you too have a responsibility to work with electricity safely. We all must consider electrical safety in offices, shops, and cafes.
- Hire industry: If you hire electric equipment, you have some responsibilities. You need to visually inspect the equipment before every hire and electrically test it at regular intervals.
Who can perform electrical test and tag?
You may require a fully qualified electrician to test and tag, but not necessarily.
- Competent person: AS/NZS 3760:2022 defines a “competent person” as someone with the appropriate knowledge and skills to conduct tests and tags. This can be obtained through an authorised test and tag course.
- Training is necessary: You do not have to be an electrician, but you must receive proper training. A quality test and tag course will instruct you in visual inspection using a PAT tester and acquaint you with relevant standards.
- Queensland regulations: Queensland is a specialty license provision. You’ll need a restricted electrical contractor’s licence to offer test and tag as a service.
What equipment needs to be tested and tagged?
Anything with a plug and an electric lead, other than low-voltage appliances (less than 50V), must be tested and tagged.
- Routine items: Extension leads, power tools, domestic appliances (kettle, toaster, microwave), portable RCDs, and even desk lamps.
- Class I and Class II: Class I appliances are earthed (such as your kettle), and Class II are double insulated (usually marked with a square inside a square). Both need testing.
- New equipment: New equipment is not subject to electric testing but must be visually inspected and marked.
How often should electrical test and tag be performed?
Test frequency depends on the environment in which the equipment operates.
- Risk-based method: High-risk areas, like building sites, must be tested more often (typically every three months). Low-risk areas, like offices, may only need to be tested every 12 months.
- AS/NZS 3760:2022: This standard guides the frequency of testing. It is recommended that one become familiar with the advice.
- Best practice: Although you are not necessarily legally required to test at some frequency, it is always better to err. Regular testing is a small cost that will make you an absolute burden to yourself in the future.
Case study
Developing a case study gave me valuable knowledge regarding how Melbourne businesses manage electrical safety compliance. Through their electrical test and tag service, fire extinguisher testing, RCD testing, and emergency and exit light testing, they provide services to business owners, facility managers, and health and safety officers who need to uphold high levels of safety.
The study focused on the role of proactive compliance in reducing workplace risks and enabling business continuity. Most organisations overlook regular testing, leading to safety hazards and non-compliance penalties. Through innovative education and bespoke provision of services, Hashtag Safe Work can bridge this gap and ensure businesses are compliant and safe. This case study yet again demonstrated the worth of content that speaks directly to the concerns uppermost in decision makers minds and provides them with certainty with what they need to get workplace safety and compliance on the agenda.
Conclusion
Electrical tests and tags are vital aspects of workplace safety. It will prevent accidents, keep you within the law, and give you a sense of security in knowing your workers are safe. Don’t wait for something to go wrong. Proactive electrical safety management, including regular electrical test and tag, is a wise investment in your business and, more importantly, in the safety of your people.
